Несмотря на то, что первой технологией аддитивного производства, примененной для создания металлических трехмерных прототипов, стал метод экструзионного послойного наплавления (FDM), наибольшую популярность при производстве металлических деталей завоевали технологии лазерного и электронно-лучевого спекания и плавки. Первопроходцем и лидером по производству аппаратов для аддитивного производства методом «электронно-лучевой плавки» (EBM – Electron Beam Melting) стала шведская компания Arcam. Компания была официально основана в 1997 году, но рождению коммерческого проекта предшествовали четыре года исследований, проведенных совместно с учеными из Технического университета Чалмерса в Гетеборге. Фактически, EBM основана на том же принципе, что и технология лазерной плавки, за исключением использования электронных пучков высокой мощности вместо лазерных лучей. В целом, электронно-лучевая плавка несколько более сложна, чем лазерная, но обладает более высоким производственным потенциалом. Компания Arcam добилась широкого успеха среди производителей ортопедических имплантатов и авиационных деталей. Ортопедические имплантаты, изготовленные методом EBM, привлекательны не только прочностью, легкостью и износоустойчивостью используемых титановых сплавов, но и возможностью создания полых или пористых металлических структур. Подобная архитектура напоминает строение костной ткани и способствует остеоинтеграции, то есть сращиванию костных тканей с имплантатом аналогично натуральному физиологическому процессу. Что же касается авиационной и нефтегазовой промышленности, электронно-лучевая плавка позволяет создавать жаростойкие форсунки и лопатки газовых турбин, включая реактивные двигатели. Кроме того, метод успешно используется для создания несущих титановых элементов крыла. 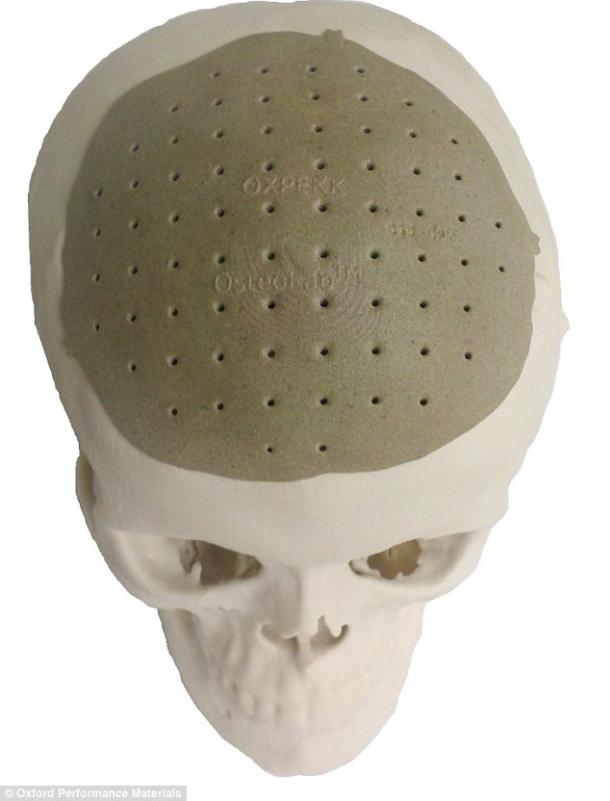 Аддитивное производство привлекло внимание и космической отрасли, включая НАСА. В первую очередь это касается разработки систем космических аппаратов и ракет-носителей. Ярким примером можно считать использование технологий лазерной и электронно-лучевой плавки для создания элементов ракетных двигателей: камер сгорания и форсунок со стойкостью к температурам свыше 3000°С. Высокое давление и температура требуют использования тугоплавких и прочных материалов – таких, как титан. Аддитивное производство же не ограничено геометрической сложностью изготовляемых деталей – практически любая форма может быть выполнена без необходимости последующей сборки или сварки. Единственным реальным ограничением является размер рабочей камеры печатающего устройства. В то же время, конструктивных ограничений по размеру рабочей камеры не существует. Вопрос лишь в спросе на технологию, ведь такого рода устройства весьма дороги, а чем больше, тем дороже. Тем не менее, китайская компания Nanfang Ventilator Co., Ltd уже берется за создание промышленных печатных устройств аддитивного производства крупногабаритных металлических деталей – вплоть до шести метров в длину и весом до 300 тонн! Но при всех достоинствах традиционной лазерной и электронно-лучевой плавки, амбиции НАСА привели к тому, что даже эти новаторские технологии оказалась недостаточны. Дело в том, что инженеры НАСА предложили рассмотреть возможность применения аддитивного производства на орбите. С точки зрения снабжения, идея абсолютна логична. Зачем везти с собой набор запасных деталей или ждать доставки с Земли при экстренной ситуации, когда те же детали можно произвести на орбите? И здесь НАСА столкнулась с серьезной проблемой: как мы уже выяснили, традиционный метод электронно-лучевой плавки подразумевает использование порошкообразного расходного материала, и не только для создания самой детали, но и использования в качестве поддерживающих слоев при печати деталей сложной формы. Но как удержать порошок на месте в условиях невесомости? В итоге, инженеры НАСА решили позаимствовать конструктивный элемент привычных экструзионных 3D-принтеров – подачу расходного материала в виде нити или проволоки. И если использование экструдера для подачи расплавленного тугоплавкого металла непрактично ввиду сложностей с нагревом головки до необходимой температуры и бесперебойной экструзией, то бомбардировка расходного материала электронным пучком вполне подходит для плавки материала в точке соприкосновения с моделью. Кроме того, устраняется и необходимость очищать готовые модели от остаточного материала, что в условиях невесомости опять-таки было бы проблематично. Новая разновидность электронно-лучевой плавки получила название «производства произвольных форм электронно-лучевой плавкой» (EBFȝ - Electron Beam Freeform Fabrication). Кроме возможности функционирования в условиях невесомости, технология EBFȝ обладает еще одним важным преимуществом над своими предшественниками – возможность одновременной печати разными материалами. Использование нескольких экструдеров может даже позволить создавать электронные и электромеханические компоненты благодаря попеременной печати керамических/пластиковых и металлических слоев. В случае успеха, разработчики невольно приведут к логическому завершению программу RepRap – проект создания устройств, способных воспроизводить самих себя. Практической же целью проекта является возможность производства всех необходимых устройств в открытом космосе или даже на поверхности других планет, используя только местные материалы. В частности, аддитивное производство может стать ключевым фактором в создании постоянных колоний на Луне и Марсе. А каковы перспективы аддитивного производства с использованием металла на Земле? Несомненно, отрасль будет развиваться. В последнее время данные технологии привлекают внимание промышленных гигантов – таких, как Boeing, General Electric, Lockheed Martin, Mitsubishi, General Motors. Экономичность и практичность – два качества, которые не могут быть не оценены по достоинству. В некоторых случаях использование технологий спекания и плавки уже достигает больших масштабов: по словам представителей компании Arcam, произведенные ими устройства были использованы для создания более 30000 титановых имплантатов для реконструкции тазобедренных суставов. И это всего лишь начало. Единственным сдерживающим фактором является себестоимость. Стоимость устройств, несомненно, снизится в соответствии с повышением спроса. Однако сам спрос регулируется достаточно высокой ценой некоторых расходных материалов. Но есть хорошие новости: компания Metalysis недавно обнародовала планы по постройке фабрики для производства титанового порошка, применяемого в аддитивном производстве. Стоимость проекта оценивается в 0млн, что говорит об огромном интересе со стороны промышленности и инвесторов. На данный момент титановый порошок продается по цене от 0 до 0 за килограмм, что не идет ни в какое сравнение с алюминием по цене - за 1кг. Соответственно, объем производства титана в 2012 году составил всего 140000 тонн, в то время как алюминия – 48млн тонн. Metalysis прогнозирует возможное снижение стоимости титанового порошка на 75% благодаря применению новаторской электролитической технологии производства. Нетрудно догадаться, что существенное снижение стоимости высоко востребованного титана приведет к значительному росту спроса на 3D-печатные устройства, способные воспроизводить металлические модели. Двумя компаниями, которые выиграют от такого развития событий больше всех, станут 3D Systems и Arcam – лидеры по производству лазерных и электронно-лучевых устройств, соответственно. 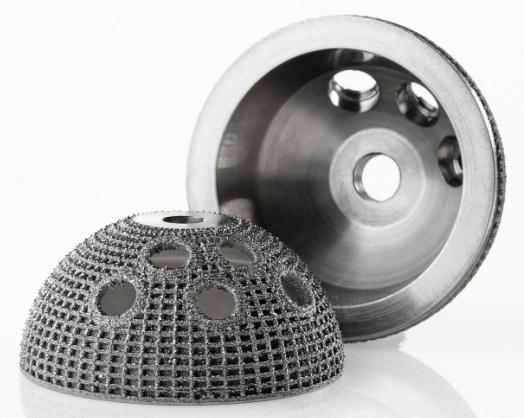 Вполне возможно, что повышенный промышленный спрос на устройства для лазерной и электронно-лучевой плавки сделает данные технологии доступными и для бытового использования. Технология EBFȝ даже обладает необходимым потенциалом для создания полноценных «домашних фабрик». Если сделать настенный крючок для половника уже не представляет никаких трудностей для обладателя бытового 3D-принтера, то EBFȝ сможет создавать не только пластиковые крючки, но и сами стальные половники, причем с пластиковой ручкой. Более того, печать электронных и электромеханических компонентов фактически ограничит возможности пользователей их собственной фантазией, а заодно создаст сущий кошмар для производителей по всему миру. Если соблюдение авторских прав уже становится проблемой, то полноценная печать с комбинированным использованием пластиков и металлов может теоретически позволить создание почти любого устройства. Конечно же, такой уровень останется недостижимым еще долгое время, и не только потому, что сама технология 3D-принтеров, печатающих металлом, достаточно малоразвита, но и ввиду недоступности определенных материалов: мало кто сможет достать порошкообразный германий для производства трансивера сотового телефона С другой стороны, пластика и стали вполне хватит для создания полноценного огнестрельного оружия, тем более что компания Solid Concepts уже создала прецедент в виде металлической реплики пистолета Colt M1911, а Пентагон рассматривает возможность печати оружия на кораблях экспедиционных групп, вместо дорогостоящей доставки к театру действий из США. США и Великобритания уже приняли законодательные меры по запрету нелицензионного производства оружия с помощью 3D-печати. Как сильно соображения безопасности повлияют на развитие бытового применения технологии аддитивного производства, покажет лишь время.  2843 |